
「新型アクセラのリアサスペンションは、トーションビーム(TBA)になる」
MAZDA SKYACTIV Gen2の最初の一台であるアクセラのサスペンション形式がわかると、自動車業界では一つのネガティブな話題になった。多くの自動車ファンは、「コスト優先のTBAかよ」とか「マツダは終わった」と予想通りの反応を口にするようになったし、ジャーナリストや専門家ですらマツダの技術者の意図を正しく捉えられた人は少ない。
SKYACTIVE-Xエンジンとボディデザインの方は、わかりやすい話題になったので、多くの人が認識しているが、SKYACTIV ビークル・アーキテクチャーを理解しようとする人はほとんどいないし、SKYACTIV Gen2を理解しようとする人はもっと少ない。
今日は、Gen2の新TBAサスペンションに隠された秘密を探っていくことにする。

SKYACTIV Gen2試作車
■現在のマツダの状況
技術論に入る前に、マツダの経営戦略とGen2は大きな関連があることを先に理解しておきたい。
今日は、マツダの経営分析の話をするつもりはないが、マツダの経営は安泰というわけではなく、北米では自信のあるCXシリーズでさえ、多額の販売奨励金を投じないと数が売れないことが大きな衝撃になった。つまり、他社よりも魅力のあるクルマをよりアフォーダブルに提供する必用があり、さらにトランプ政権の政策を見れば、日本で作って輸出するというビジネスモデルには、大きなリスクが存在することが明白だ。マツダの次期戦略におけるSmallモデルの中心的な車種であるMazda3は、ライバルより魅力的でお買い得なだけでなく、日本、北米、メキシコ、タイの工場で生産・販売できる設計のクルマでなければならない。
※注:2018年1Qの北米の売上状況は、新型CX-5、CX-9が前年比20%以上増加して、前年度21.8%増 販売管理費の使途状況は不明

北米仕様 現行MAZDA3
■なぜTBA形式をを選んだのか
サスペンションの目的は、路面や状況の変化に関わらず、タイヤの接地面変化を起こさず安定して路面に密着させ、路面からのショックの入力を吸収していなすことだ。 もしTBAに構造が単純で解析しやすいという利点があるなら、ネガを発生する状況を把握するのはより容易になる。
サスペンションの解析でもコンピュータシミュレーションが決定的な役割を果たした。MBD(Model Based Development)の活用である。得意とするジャンルを限ってやればやるほど、コンピュータの能力を生かすことができる。スーパーコンピュータに過度な期待をしてもだめで、コンピュータの計算は、人間が想定できている世界(モデル)の中で繰り返し高速計算をして最適解を出すのだから、MBDで解析するならば、要素は少ないほど早く最適解に達する。というのは当然のことだ。
サスペンションのタイヤ取り付け部分の剛性を格段に上げてやり、タイヤの左右間を結ぶ鋼材を「適切な厚さ」で仕上げて、力のかかる向きと速度を理想通りにコントロールするには、どういう形状が必要なのかをMBDで求めたのだ。 「商品力が下がる」という指摘は理解している。しかし、マツダの次の戦略である、Small Vehicleグループを成立させるには、軽量で構造が単純ながら、次世代の走りを実現できるサスペンション構造が必用なのである。 カタログに「前後ダブルウイッシュボーン」と書くよりも、ネットの口コミに、「新アクセラの乗り心地はすごく良い」と書かれる方が実は効果的なのだ。

SKYACTIVE ビークル・アーキテクチャーによる、サスペンションの役割
■サスペンションに期待すること
Gen2では、従来のバネ上へ伝わる力の大きさ(最大値)を衰滅させて低減する考え方から、バネ上へ伝える時間をコントロールして遅れなく滑らかにする考え方に変わった。 たとえば前輪が突起物を踏んだ場合、従来よりも早くタイヤを動かして力全体を滑らか吸収するようにしたいということだ。 巨大な重量を持つジェット機が着陸する時に、着地速度を調節して滑らかに滑走路に接地する方法と同じ考え方である。

シャシーの進化(新Mazda3シャシー)
この目的達成するには、3つの課題を解決せねばならない。
①路面から受けた力によるサスペンションの支持剛性部分のブレをなくす。
②タイヤの上下バネ運動を低減した上で衝撃を吸収する。
③②と同時に上下の入力をより早く適切な時間で滑らかに増加させるるために
サスペンションの取り付けアーム角を拡大し、接地面を適切に制御する。
「本当にTBAでは、タイヤの位置決めと振動遮断の両立はできないのか」
という疑問から、Gen2のサスペンション形式の議論は始まった。
■TBAの長所と短所
サスペンション形式に、マルチリンクなどの複雑なリンクを持つ構造を用いるのは、様々な車両の状態に対してタイヤを接地させるバリエーションが多く取れるからである。 一方で、リンクが増えるとそれらを接続するブッシュのゴムの遅延が発生するので、情報の伝達速度も遅延するという欠点がある。また、リンクの設計を誤ったり、時系列を経ることでこれらのリンクの組み合わせにずれが発生すると想定外の動作をしてしまう。 これを封じるためにレースカーなどでは、乗り心地や路面の荒れへの追従性を無視して金属ピロボールを使って遅延とずれを防ぐわけである。 マツダだけでなく、他社も複雑なマルチリンクの構造に発生する様々な応力変化をスーパーコンピュータでモデルをでシュミレーションして、適正化を図って設計しているけれど、要素が多いがゆえに千差万別な組み合わせを解析し、最適解を求めることは容易ではない。
一方で、トーションビーム方式は、左右のタイヤが組み付けられているトレーリングアームを、センタービームという「棒」で結ぶという単純な構造なので、部品点数が少なく軽量で、力のかかる方向が集約しやすい。その代り、TBAは前側のブッシュにリヤタイヤの正確な位置決めと振動遮断という相反する機能が求められるから、大抵はどちらも中途半端なサスペンションになる。

トレーリングアームへのセンタービーム取り付け位置の最適化の図
マツダは、現行SKYACTIVEで地味に、トーションビームを改良している。現行デミオで、トレーリングアームのボディとの付け部分の角度を改良している。左右のトレーリングアームが接続する箇所だから、振動を制御するキーポイントである。ここには接続のゴムブッシュがはめてあって、ボディとつながっているわけだが、後輪が路面のギャップを踏んだ際に後方に動くように取り付け位置を変更している。この結果、ボディに伝わるショックを25%低減した。ならば、突き上げの吸収のために犠牲になっていた、ダンパーの縮み側の衰滅力を元に戻してやることができる。 ギャップを踏んだショックは、一度後方に逃げて、リアボディとセンタービームがゆがむことで吸収するので、上下の振動は素早く止めても、突き上げには影響しない。

取り付け角度(すぐり角だけ)の変更状態
日本車の多くは、ユーザ様からの「突き上げがー」の声が怖くて、縮み方向の衰滅力を落として、びよーんとリアをゆっくり戻す設定にしている。(自動車メーカー側も愚かな設定だとわかっているけれど、お客様の声だから仕方ない)現行デミオはこの悪癖から解放され、前後ダンパーの縮み側の衰滅力を高めることができて、サスペンションの上下振動を素早く止めることができるようになった。
SKYACTIVE Gen2がTBAを装備しても、伸び方向、縮み方向のいずれにも自由な設定ができるわけで、SKYACTIV ビークル・アーキテクチャーを実現する上で、TBAではできないという理由が一つ減ったのである。
■TBAを改良する
TABの取り付け角度を最良にすることで、ダンパーの伸び、縮側の設定を理想的な方向へと変更できることがわかった。次は、トレーリングアームの中心的な部品であるセンタービームの改定だ。
センタービームの主たる機能には、
①タイヤを支持する機能
②車両のロール姿勢を制御する機能
の二つがある。理想的な形とは、両端のトレーリングアームとの接続部は、曲げ剛性を高く(変形しづらくがっちり固めるということ)設定することが有効なので、結合部断面を大きくしたい。 一方で、ロール姿勢を制御するには、ねじり剛性をクルマの特性にあった適切な値に合わせて、端から中央部の断面の大きさを決める必要がある。
ここまでわかったら、クルマの妖精に何をお願いしたらいいのだろう。
「タイヤの位置決めを正確にするために、タイヤついているトレーリングアームをがっちり固定した上で、同時に、センタービームの端から端まで使ってうまいこと振動をボディに伝わる速度を調整してください。できれば、その過程で振動も吸収してくれちゃってもOKです。」
とお願いすればいいのだ。
名前は、Smart Expand Beam(SEB)としよう。 と名前と理想の形は決まった。

つまり、こういう感じにSEBを整形できればいいんじゃないかと。
Gen2のサスペンションのポリシーは、「振動を適切な速度で伝達する」だったから、タイヤから入力された振動を伝える棒の直径を適切に変えてボディに伝わる振動の速度を調整できるように最適な形を計算すればいいわけだ。どう考えても、まっすぐな棒の形状のはずはなく、直径が滑らかに変わっていく形状になるだろうということは想像に難くない。
そこで、棒の太さの加減を、MBDで集中計算させて、その図面の通りの棒を作ることにする。
では、在来型のセンタービームと形状を比較してみよう。

在来式: クラッシュドパイプ式センタービーム
DJデミオに採用
鋼管から形状を変更することで各断面を成形した中空断面のパイプの真ん中を潰して接続する方法で、使用するパイプ径は、ロール姿勢の大きさに合わせたねじり剛性にあったパイプ径を使うことになる。ロール剛性を得る代わりに、トレーリングアームとの結合部分の曲げ剛性の大きさは、パイプの直径で決まってしまうので、どうしても端っこがヨワヨワになり、タイヤのついたトレーニングアームは好き放題な方向に動いてしまう。

新型:可変直径センタービーム と在来式の比較
上段の図の構成が現行DJデミオ、下段の図の構成が次期アクセラに採用されたSEB
新しいセンタービームは、ロール剛性に合わせた中央部のねじり剛性を確保した上で、センタービームとトレーリングアームとの結合部分の断面前後幅を拡大した。つまり、人間の骨と同じように、両端を太く丸く、中央を幅広くする形状の筒にしたわけだ。

可変直径センタービーム (SEB)
タイヤの両端を結ぶ棒がアーチ状に変化しているのが分かる
では、両者にどのような差が出るのか、比較してみよう。
直管とSEBの二つのセンタービームの各部位のZ軸まわりの、「部材の変形のしにくさ」(材料工学では、断面二次モーメントと言う)の比較を示す。
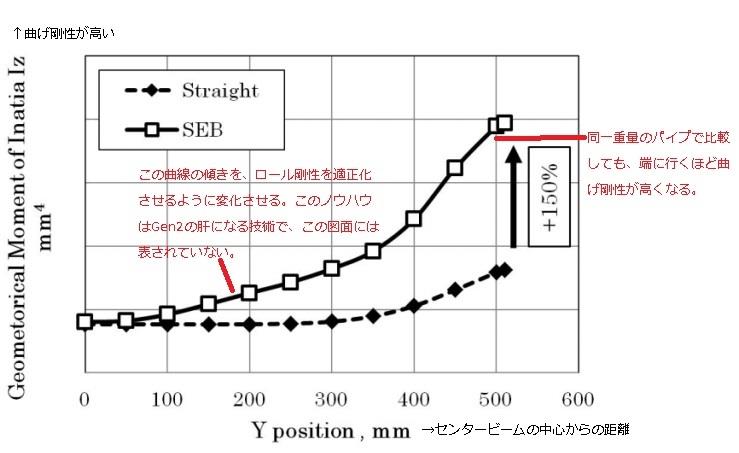
SEBと直管の断面二次モーメントの差異
(2本の管は、同じねじり剛性と質量である)
SEBは、直管に比べて、中央部からトレーリングアームとの結合部分に向けて剛性を増加させることができており、結合部近傍での部材の変形しにくさを同等重量で1.5倍にしている。(これは、比較図であって、実際に採用されるSEBは、材料と構造の見直しにより、より断面二次モーメント値が高い物が使われる)
同時にこのグラフは、各部の剛性をどのように設定すれば、理想的に振動を吸収できるかをも示している。振動の吸収を理想的にするには、直線的に直径を変化させるのではなく、偏微分方程式で示される線形で変化させていくわけである。この妙な形状が、Gen2のキーである。 現在でも、この形状の理想を求めて日々改定が繰り返されており、発売までにより理想に近いセンタービームを作ろうと改定が続いている。

SKYACTIVE Gen2サスペンションの実車構造(試作車)
こうして出来上がったりサスペンションは、剛性あふれるかっちりしたものではなく、人間の筋肉のように、「やわらかで力強い」構造に仕上がっている。 両端はしっかりと固定し、中央部は上下、左右に計算道理にたわみながら振動を吸収していく。新TBAを人間の構造に例えるなら、新しいセンタービーム(SEB)が骨であり、タイヤ、ダンパー、バネが筋肉の役割を果たすのだ。そのため、GEN2用のタイヤは、サイドウオールやトレッド面が柔らかい専用設計のタイヤを必要とする。 人間の体は、鋭敏性よりも正確性を重視して設計されている。GEN2もまた、この原則通りに作られている。 現在のSEBが最終回答というわけではないが、人間の生命に時間の限りがある以上、現時点で計算可能なモデルで最適解を求める方が、想定数値で複雑な機構を使うより早く正解に近い所にたどり着けるというわけだ。 よりコンピュータの解析能力が進化した時代の未来のモデルでは、さらに進んだサスペンションが設計されるだろう。

新Mazda3
■どうやって量産するのか
可変直径・形状パイプを使えば、理想的に剛性をあげられることはわかったが、どの会社もこんなことをしていないことには、理由がある。試作品ならば、鍛造の太い鉄の棒に穴をあけて、ガリガリ削って作ればいいわけだが、こんなものをどうやって量産すればいいのかということが、量産車における課題である。
パイプを作るには、鍛造した丸棒に穴をあけるか、板を丸めて溶接するかである。しかし、どちらの方法であっても、同一パイプ内の直径を変化をさせる加工は容易ではない。 また、硬い鍛造品に穴をあける加工は、簡単なことではなく、生産コスト的にも厳しい。 世界中の工場で生産するMazda3なのだから、特殊な生産設備も使えない。
要するに、
「板曲げ溶接成形の生産性を維持し、在来のプレス機を使ってSEBを製造せよ」
と、言うのは簡単だが、実行することがさらに難しい課題が現れたわけだ。
生産工程に関する話は、金属加工の話になって興味がないと思うので省略するが、以下のブレイクスルーで安定した品質の中空の棒を作り出す生産方法を実現している。学術的用語を排して書くと下記のような説明になる。
1.可変形状の棒を作る際に隙間を完全密着した後に発生する弾性回復による隙間発生を最小化する数値を見出した。
2.隙間部分を埋めて、が溶接品質を確保するための「溶接のりしろ」を加えた断面形状とのりしろ幅を見出した

製造方法:3回に分けて折り曲げ、のりしろをきれいにつなげて溶接する。
このように、Small Vehicleに搭載するSKYACTIVE Gen2サスペンションは、新しいポリシーに基づいた構成と、世界中の工場で量産できる汎用性を達成したのである。

新Mazda3
新TBAの製造においては、工場の生産設備を大きく変えることなく、組み付け方法も在来のTBAと同様なので、車両組み立ての生産性もこれまでとは大きくは変わらない。(無論、マルチリンクよりも生産性は高い)新Mazda3は、デザインとエンジンの話題が先行しているが、Small モデル用のサスペンションの完成度にも注目したい。